As of the end of September 2018, many important items of the project have been put into operation, such as the operator's house, which has been in operation since June 2018, and the electric motorbike factory area which has had trial production. from August 2018.
After one year since the start of construction in September 2017, the VinFast automobile and electric motorbike factory complex in Dinh Vu - Cat Hai industrial park (Hai Phong) has completed many important items. important.
The complex is built on a 335ha land area, including: Operating House, Electric Motorcycle Factory Area, Automobile Factory Area, Supporting Industrial Park, Training Center, Research and Development Institute. Development (R&D).
Panorama of VinFast complex with a scale of 335 hectares.
Main gate of VinFast complex.
The factory campus has a lot of green trees.
The design capacity of the complex is 250,000 vehicles/year in phase 1 and 500,000 vehicles/year in phase 2 for cars. With electric motorbikes, the capacity is 250,000 vehicles/year in phase 1, increasing to 500,000 vehicles in phase 2 and can be expanded to 1 million vehicles/year.
VinFast products include: 5-seat cars (Sedan), Cross-country sports cars (SUV), Small cars, Electric cars, Electric motorbikes and Electric buses.
According to the plan, VinFast will launch electric motorbikes at the end of 2018, 2 internal combustion engine car models (5-seat Sedan and 7-seat SUV) in the second quarter of 2019, 1 electric car model, 1 small internal combustion engine cars and electric buses by the end of 2019.
Executive building and training center.
Main lobby of the executive building.
Factory area for producing electric motorbikes
As of the end of September 2018, many important items of the project have been put into operation, such as the operator's house, which has been in operation since June 2018, and the electric motorbike factory area that has had trial production. from August 2018.
Welding workshop
Designed by the world's leading consulting company from Germany, Durr, and installed by general contractor WELCOM. The line is designed with European standards for working environment and safety level of frame welding stations.
100% of the electric motorbike frame welding process is welded by ABB Robots, no manual processing. 95% of production line equipment is imported from Europe by world-famous brands such as ABB, Frorious, ItalMeg.
The welding line has a total of 25 automatic welding robots with CMT welding technology with less spatter and less welding slag to ensure weld quality penetration.
Paint shop
Designed by the world's leading consulting company from Germany, Durr, and installed by general contractor Combat. The line is designed with European standards for working environment and safety.
Including two lines for painting plastic and painting electric motorbike frames, 95% automated using German technology to save energy and European quality.
In particular, the paint factory has the best environmental and waste treatment system in Asia today due to the use of the most advanced exhaust and wastewater treatment technology available today.
Paint workshop area.
Assembling workshop
Designed by the world's leading consulting company from Germany, Durr, and installed by general contractor Maruka. The line is designed with European standards for working environment and safety.
The entire line is imported from Japan to ensure the highest quality. VinFast's assembly line can be considered the most modern in the region with technology and equipment provided by European companies such as ABB, Atlas copco...
The line is quality controlled based on modern automated torque control devices, to prevent defects during the production process.
The finished vehicle inspection equipment system is imported from Italy with high quality and connects all production and process quality data managed on the server, helping VinFast analyze and evaluate to prevent defective products. out on the market
Automobile factory area
The Body workshop, Paint workshop, Engine workshop, Assembly workshop and Support workshop have been completed and are in the process of installing machines, the Stamping workshop will be handed over in October.
Stamping Workshop
Area: 50,000 m2
Stamping capacity: 16 parts/minute
By monitoring the production process according to the technology of SCHULER company (Germany), data on the technical parameters of the Stamping factory will be collected online during the production process from the equipment. installed in the line.
Vehicle Body Welding Workshop
Area: 100,000 m2
Capacity: 38 vehicles/hour
VinFast car body welding workshop is designed and supplied with production lines by leading partners such as FFT, EBZ, HIROTEC, and is equipped with about 1,200 robots manufactured by ABB. When put into operation, this will be the most modern, fully automated car body welding factory in Vietnam and Southeast Asia.
Some factories have a scale of up to 10-20 hectares.
Paint shop
Area: 25,000 m2
Production capacity: more than 800 vehicles/day
Dürr's EcoSmart VEC smart air management system from the Federal Republic of Germany operates fully automatically, providing energy on demand through recording real production parameters. This technology helps significantly reduce gas and electricity consumption when drying newly painted vehicles.
Engine manufacturing workshop
Area: 50,000 m2
The workshop is designed and supplied with production lines by leading partners such as GROB, Thyssenkrupp, AVL, MAG, using the latest precision mechanical technology to process engine heads, engine bodies and crankshafts. muscle. In addition, the workshop also has an engine quality testing line (Hot test and cold test) to ensure 100% of products are quality controlled from the source. Processing machines are equipped with 4.0 technology with many features such as: real-time control of machine status via smartphone, remote control at night or on weekends, real-time machine error analysis, etc.
Vehicle assembly and finishing workshop
Area: 200,000 m2
The line is designed and supplied by the leading supplier from the Federal Republic of Germany, Eisenmann, with a high level of automation with conveyors and self-propelled vehicles operating interoperably with each other. In addition, the assembly stages are equipped with Atlas Copco's modern torque guns that are interlocked with the production line to ensure that the tightening force of each assembled detail is controlled and can be retrieved at all times. . Flexible production line for many product lines with quality attached to the production process.
Support Workshop
Area: 20,000 m2
The production workshop includes painting plastic parts (front bumper, rear bumper) with environmentally friendly paint technology provided by supplier Durr from the Federal Republic of Germany. In addition, the workshop also has an area for complete tire mounting and has expanded capacity for molding plastic parts in the future.
Supporting industrial park
VinFast established a supporting industrial park, accounting for about 30% of the complex area to produce components and accessories for cars and motorbikes. In addition to 100% self-investment, VinFast offers forms to call for investors in the "Supporting Industry" zone including:
Joint venture with flexible capital contribution ratio, depending on the investor's ability and intentions.
Investors provide technology, VinFast invests in infrastructure and production machinery and equipment.
Investors can invest 100% capital, VinFast provides factory space.
Training center
VinFast training center opened on September 10, 2018, with 200 students in the first course. The program includes two main fields of study: Industrial Mechanics and Mechatronics. Students receive a monthly salary during the 2.5 years of study with a "dual" training program - theory combined with practice at a rate of 40-60% according to German standards. Upon graduation, students will receive a certificate issued by the German Chamber of Commerce and Industry in Vietnam.
Practice area at the training center.
VinFast Research and Development Institute
The Institute was established with the goal of becoming a regional Research and Development Institute, gathering experts with many years of experience in the automotive industry around the world and domestically, to undertake research and selection.
technology for VinFast's vehicle line.
In the future, the Institute also hopes to contribute to building and improving the technology foundation for the domestic automobile industry through training Vietnamese engineers to design cars according to European standards, and at the same time coordinate Collaborate with major domestic universities to conduct training programs in accordance with the actual requirements of the automobile industry.
According to Truong Luong
Knowledge young
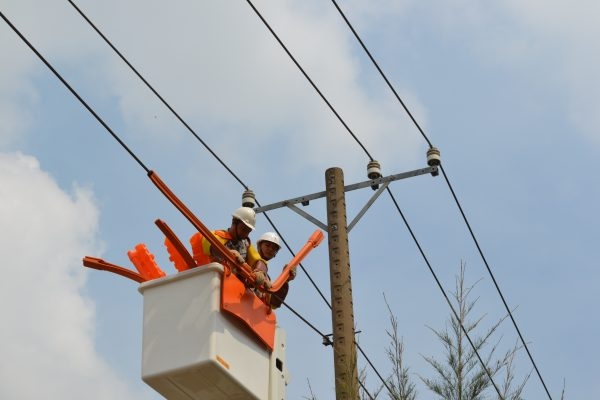
Reduce power outage time by applying new technology
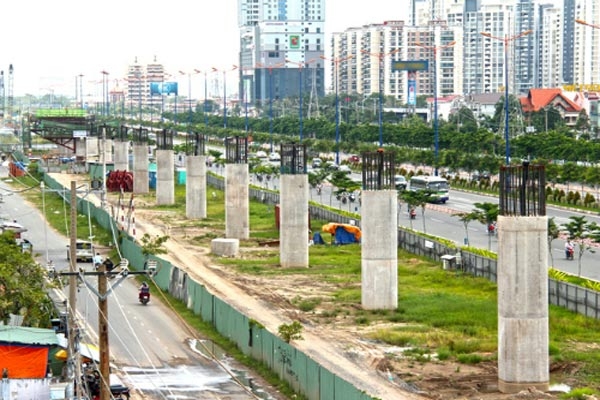
Hitachi Co., Ltd. won the bid to supply equipment for urban railway projects
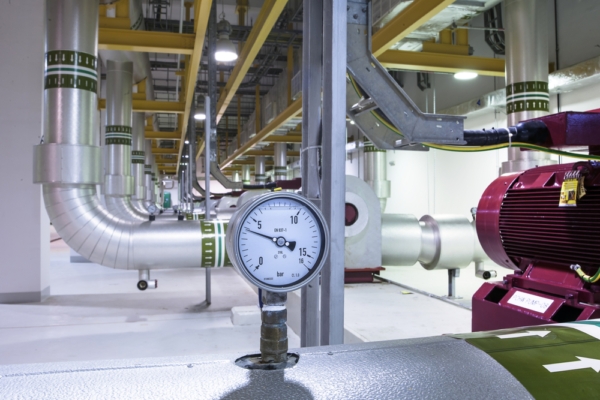
District Cooling solutions for projects
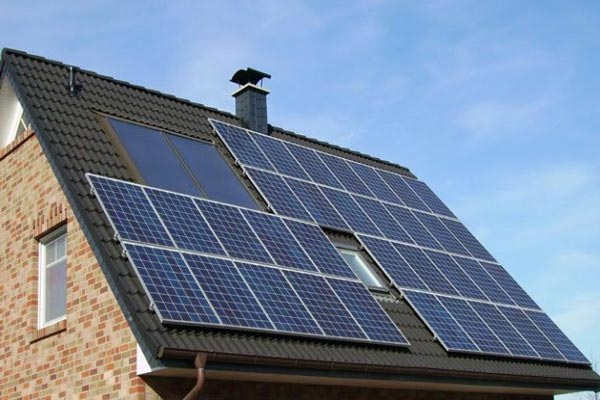
Grid-connected solar power system
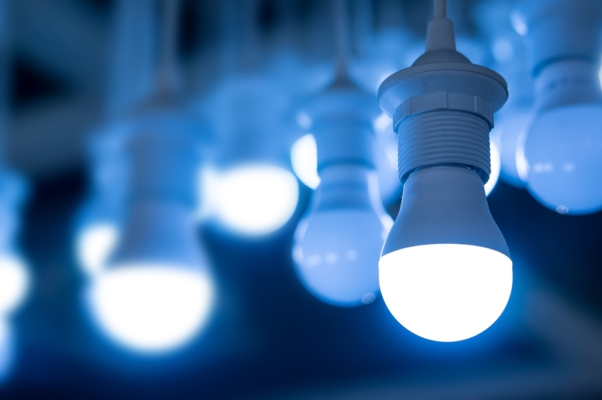
Energy saving solution with LED lighting system
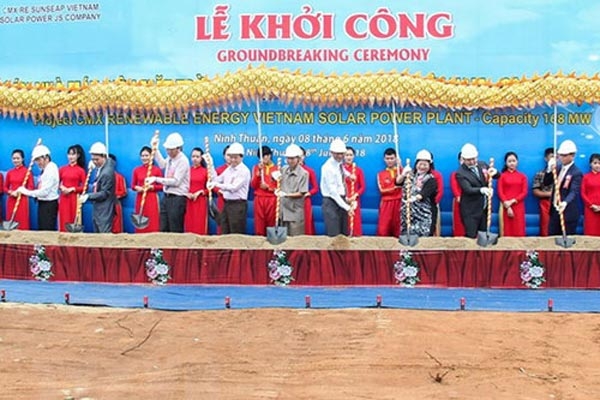
Commencement of the largest 168MW solar power plant in Ninh Thuan
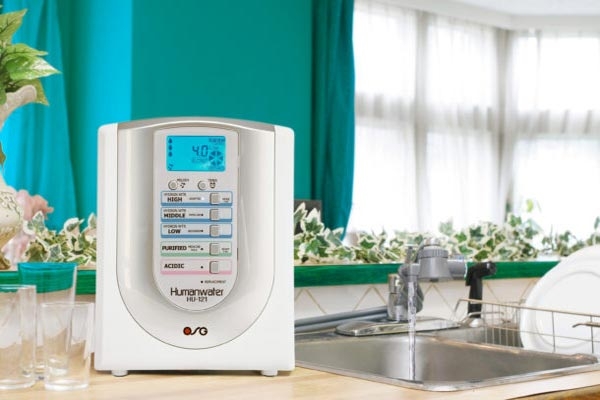
The rise of the high-end water purifier market
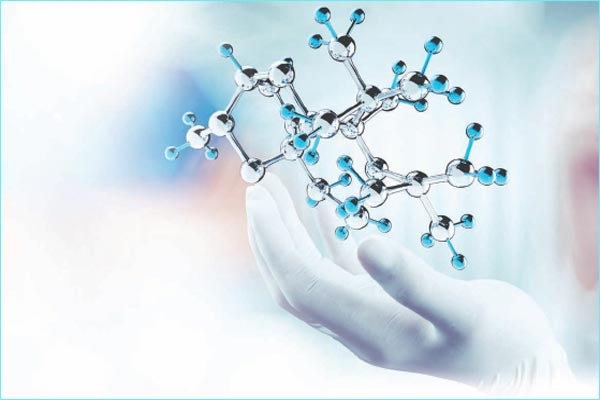
Health became the top concern of Vietnamese consumers in the second quarter of 2019
![[HTV9] New whole body disinfection solution with HClO water produced with Japanese technology](https://thanguy.com/files/news/htv9-new-whole-body-disinfection-solution-with-hclo-water-produced-with-japanese-technology-rdqcywiq.jpg)
[HTV9] New whole body disinfection solution with HClO water produced with Japanese technology
![[dantri.vn] Full body disinfection with Japanese technology, new solution for Covid-19](https://thanguy.com/files/news/dantri-vn-full-body-disinfection-with-japanese-technology-new-solution-for-covid-19-9ugqbsb1.jpg)
[dantri.vn] Full body disinfection with Japanese technology, new solution for Covid-19
![[tienphong.vn] New effective and safe solution to fight Covid-19 using Japanese technology HClO disinfectant](https://thanguy.com/files/news/tienphong-vn-new-effective-and-safe-solution-to-fight-covid-19-using-japanese-technology-hclo-disinfectant-lr7pu31d.jpg)
[tienphong.vn] New effective and safe solution to fight Covid-19 using Japanese technology HClO disinfectant
![[tienphong.vn] Special gratitude from COVID-19 patients](https://thanguy.com/files/news/tienphong-vn-special-gratitude-from-covid-19-patients-lvhjobw6.jpg)
[tienphong.vn] Special gratitude from COVID-19 patients
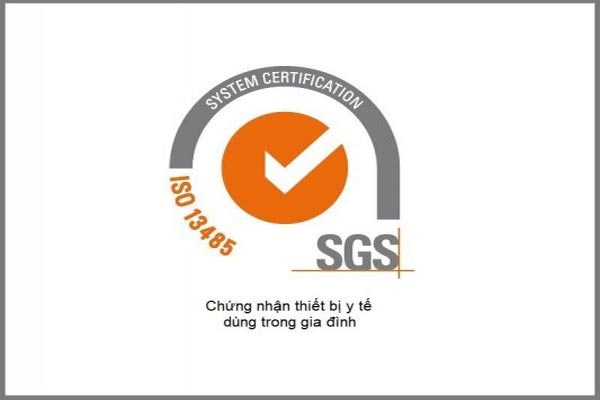
OSG electrolyte machine meets medical equipment standards for home use
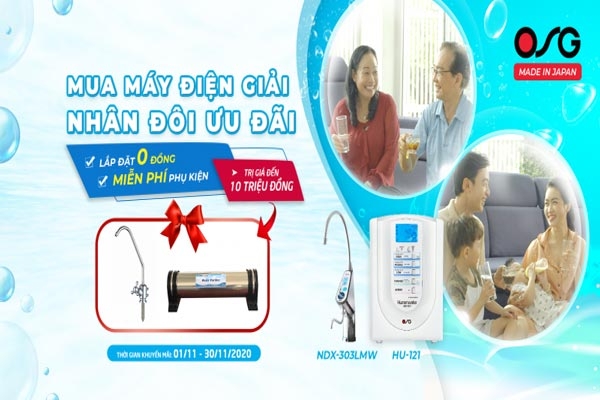
Buy an OSG electrolyte machine, double the discount with a VIP installation package of 0 VND with accessories worth up to 10 million VND
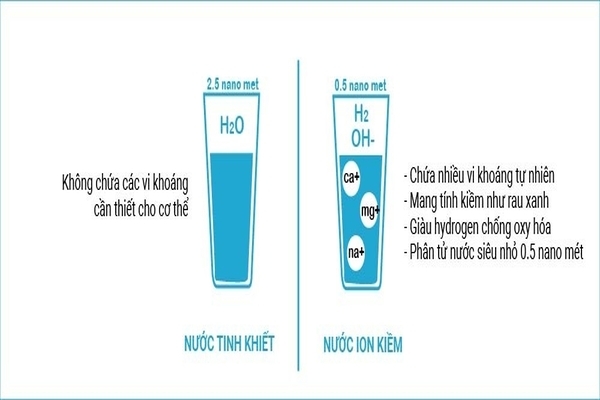